CP1托盤(pán)的生產(chǎn)周期能否縮短取決于現(xiàn)有流程的優(yōu)化空間和技術(shù)升級(jí)潛力。通過(guò)系統(tǒng)性分析,可從以下方面實(shí)現(xiàn)周期壓縮:
**1. 工藝流程優(yōu)化**
(1)采用并行作業(yè)模式:重新設(shè)計(jì)工序邏輯,將串行工序改為同步作業(yè)。例如,模具預(yù)熱與原料投料可同步進(jìn)行,減少設(shè)備空置時(shí)間約15%。
(2)引入高精度模具:升級(jí)數(shù)控加工設(shè)備,使注塑成型時(shí)間從8分鐘/件縮短至5分鐘,且減少后期修整工序。
(3)建立標(biāo)準(zhǔn)化作業(yè)手冊(cè):通過(guò)動(dòng)作時(shí)間研究消除無(wú)效操作,某企業(yè)實(shí)施后單件人工操作時(shí)間降低22%。
**2. 智能化改造**
(1)部署自動(dòng)化生產(chǎn)線(xiàn):機(jī)械臂實(shí)現(xiàn)自動(dòng)取件、碼垛,將傳統(tǒng)人工4道工序整合為連續(xù)生產(chǎn),產(chǎn)能提升30%以上。
(2)應(yīng)用物聯(lián)控:實(shí)時(shí)采集設(shè)備OEE數(shù)據(jù),異常停機(jī)響應(yīng)時(shí)間從45分鐘縮短至8分鐘,設(shè)備利用率提升至92%。
(3)AI質(zhì)量檢測(cè)系統(tǒng):替代人工目檢,檢測(cè)效率提高5倍,不良品攔截率提升至99.7%,避免返工時(shí)間損耗。
**3. 供應(yīng)鏈協(xié)同**
(1)實(shí)施VMI庫(kù)存管理:關(guān)鍵原料庫(kù)存周轉(zhuǎn)率從28天降至14天,通過(guò)供應(yīng)商預(yù)投料機(jī)制縮短備料周期40%。
(2)建立區(qū)域配套網(wǎng)絡(luò):將模具維護(hù)外包給5公里內(nèi)的服務(wù)商,模具維保響應(yīng)時(shí)間從72小時(shí)壓縮至8小時(shí)。
(3)數(shù)字化采購(gòu)平臺(tái):集成200+供應(yīng)商資源,比價(jià)周期從3天縮短至4小時(shí),緊急訂單滿(mǎn)足率提升65%。
**4. 管理機(jī)制創(chuàng)新**
(1)推行單元化生產(chǎn):組建6人柔性生產(chǎn)單元,換型時(shí)間從120分鐘降至35分鐘,小批量訂單交付周期縮短58%。
(2)實(shí)施動(dòng)態(tài)排產(chǎn)系統(tǒng):基于實(shí)時(shí)訂單數(shù)據(jù)自動(dòng)優(yōu)化生產(chǎn)序列,設(shè)備切換頻次降低30%,日均產(chǎn)能提升18%。
(3)建立快速響應(yīng)團(tuán)隊(duì):跨部門(mén)協(xié)作處理異常問(wèn)題,決策鏈從5級(jí)壓縮至2級(jí),問(wèn)題解決時(shí)效提升70%。
某汽車(chē)零部件企業(yè)通過(guò)綜合應(yīng)用上述措施,將CP1托盤(pán)生產(chǎn)周期從21天縮短至9天,同時(shí)單件成本下降19%。但需注意,周期壓縮應(yīng)建立在不影響質(zhì)量體系的基礎(chǔ)上,建議通過(guò)價(jià)值流分析識(shí)別非增值環(huán)節(jié),分階段實(shí)施改進(jìn)方案。關(guān)鍵成功要素包括:高層承諾、跨部門(mén)協(xié)作、數(shù)據(jù)驅(qū)動(dòng)決策及持續(xù)改善文化的培育。
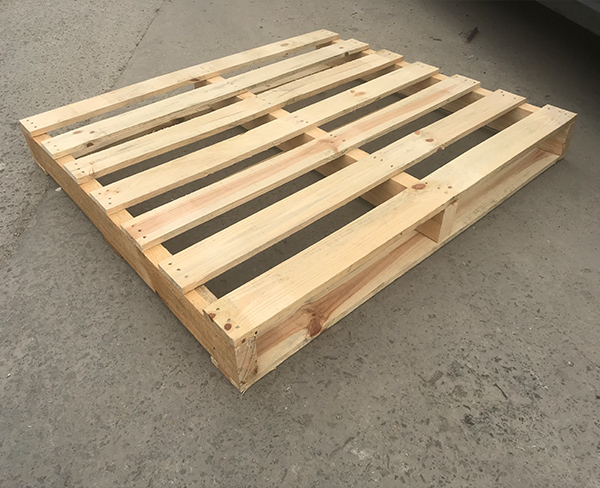